Distributed Decision-making in Disrupted Industrial Environments Using a Multi-agent Framework
Student: Mingjie Bi
The modern industrial environment is becoming more complex and dynamic, where varying uncertainties and disruptions could occur and highly impact the performance of manufacturing factories and supply chain networks. Conventional decision-making approaches lack the flexibility and agility to effectively handle disruptions. Enabled by current Artificial Intelligence (AI) techniques, multi-agent control has been proposed to conduct distributed decision-making to provide an agile response to disruptions. A multi-agent system consists of various autonomous agents, which are cyber representations of their associated physical objects (e.g., machine, supplier, etc.) and have their own knowledge and goals. Agents communicate and interact with each other to make high-level decisions for their associated physical objects. This project develops a model-based multi-agent framework to address risk management within an agile and resilient response to various unexpected industrial disruptions. The framework comprises model-based agents, heuristic-guided communication, and optimization-based decision-making, showcasing the improved flexibility, agility, and resiliency of the industrial systems.
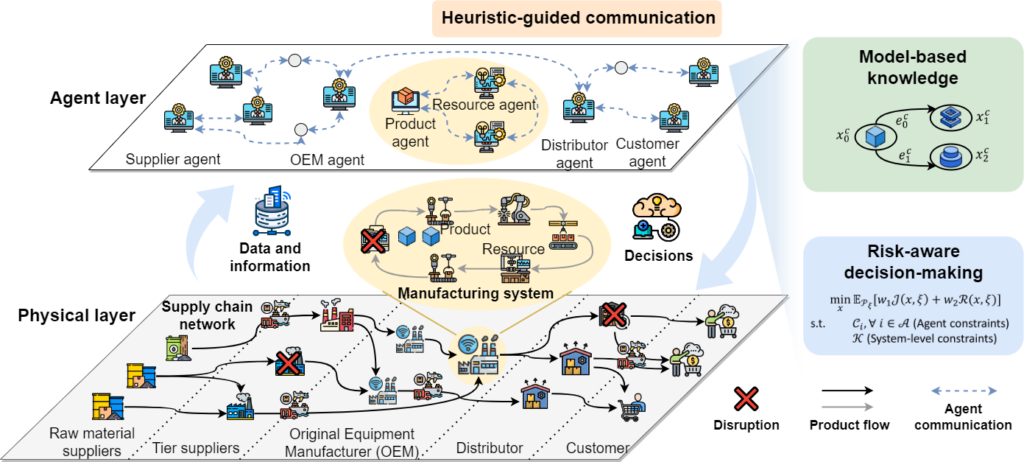
Adaptive, State-based Health Modeling for Industrial Equipment
Student: Max Toothman
Unplanned downtime due to equipment health problems imposes significant costs on many manufacturing operations in the form of maintenance expenditures and lost production. To reduce these costs, manufacturers have become interested in implementing predictive maintenance strategies that allow them to carry out equipment maintenance at opportune times and only when necessary.
This project proposes novel, state-based health modeling frameworks that facilitate the widespread adoption of predictive maintenance strategies in the industry. The research allows machine digital twins to make real-time health estimates and predictions that are informed by recent sensor measurements and prior modeling results. Adaptive, trend-based modeling methods have also been developed to probabilistically diagnose ongoing degradation processes while simultaneously detecting and characterizing anomalous machine behavior caused by novel degradation modes.
Predictive Health Maintenance for Bearings
Students: Marcus Badgett, Max Toothman
Rotating equipment is used in numerous industrial applications that desire increased system reliability. Since bearings are one of the most common components used in rotating equipment, our research aims to predictively determine the remaining useful life of bearings before the component fails. Most existing frameworks assume a bearing is operated under a single speed condition until failure. However, in practical manufacturing operations, a manufacturing component, such as a bearing, can undergo several different speed conditions before failure occurs. Thus, the project aims to develop models that adjust predictive forecasts under varying speeds.
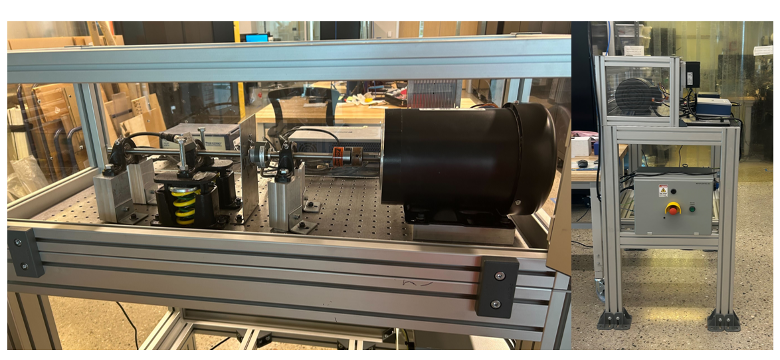